Hello riders!
It seems that moving somewhere once a year has become a tradition.
After working in Kazakhstan for a year and a half, we decided to open an additional production office in China (Shenzhen). Well, why not? It’s close by. We've been working with Chinese suppliers for quite some time and have managed to achieve consistent quality in PCB manufacturing.
We spent a long time considering which production and assembly approach to choose:
Fully outsourcing controller production and assembly to a contractor, similar to how Apple manufactures its devices at Foxconn. In this case, we would supply all the necessary components to the factory, where they would assemble the finished device. Our only tasks would be to load the firmware, package the product, and ship it to customers.
Outsourcing only the components we can't manufacture ourselves — PCBs, plastic and aluminum enclosures, and other parts — then shipping everything to our office for in-house assembly and testing. This is the model we've been using for the past six years.
After numerous tests and countless hours spent at factories, we decided to stick with the second approach, which we are already familiar with. It seems that this is the only way we can ensure the highest level of quality and reliability for our devices. The numbers speak for themselves: our in-house assembly has a 5% defect rate, while Chinese contractors reach 30%. Moreover, 4% of our defects are easily fixable, meaning that in the end, 99% of our devices work perfectly. With outsourced Chinese assembly, however, repairs are often difficult or even impossible due to severe process violations and assembler negligence.
The new office will serve as an assembly facility and a product warehouse. It will also ensure seamless logistics worldwide via UPS, DHL, and FedEx. Within a 50 km radius, numerous manufacturers are ready to produce necessary components quickly and cost-effectively. We can personally visit factories to resolve issues without lengthy WeChat discussions.
Here are some photos of our new office — a purpose-built industrial space with cargo elevators, air conditioning, ventilation, and other conveniences. It looks like a five-star hotel — the Chinese know how to create comfort for tired engineers!
After working in Kazakhstan for a year and a half, we decided to open an additional production office in China (Shenzhen). Well, why not? It’s close by. We've been working with Chinese suppliers for quite some time and have managed to achieve consistent quality in PCB manufacturing.
We spent a long time considering which production and assembly approach to choose:
Fully outsourcing controller production and assembly to a contractor, similar to how Apple manufactures its devices at Foxconn. In this case, we would supply all the necessary components to the factory, where they would assemble the finished device. Our only tasks would be to load the firmware, package the product, and ship it to customers.
Outsourcing only the components we can't manufacture ourselves — PCBs, plastic and aluminum enclosures, and other parts — then shipping everything to our office for in-house assembly and testing. This is the model we've been using for the past six years.
After numerous tests and countless hours spent at factories, we decided to stick with the second approach, which we are already familiar with. It seems that this is the only way we can ensure the highest level of quality and reliability for our devices. The numbers speak for themselves: our in-house assembly has a 5% defect rate, while Chinese contractors reach 30%. Moreover, 4% of our defects are easily fixable, meaning that in the end, 99% of our devices work perfectly. With outsourced Chinese assembly, however, repairs are often difficult or even impossible due to severe process violations and assembler negligence.
The new office will serve as an assembly facility and a product warehouse. It will also ensure seamless logistics worldwide via UPS, DHL, and FedEx. Within a 50 km radius, numerous manufacturers are ready to produce necessary components quickly and cost-effectively. We can personally visit factories to resolve issues without lengthy WeChat discussions.
Here are some photos of our new office — a purpose-built industrial space with cargo elevators, air conditioning, ventilation, and other conveniences. It looks like a five-star hotel — the Chinese know how to create comfort for tired engineers!
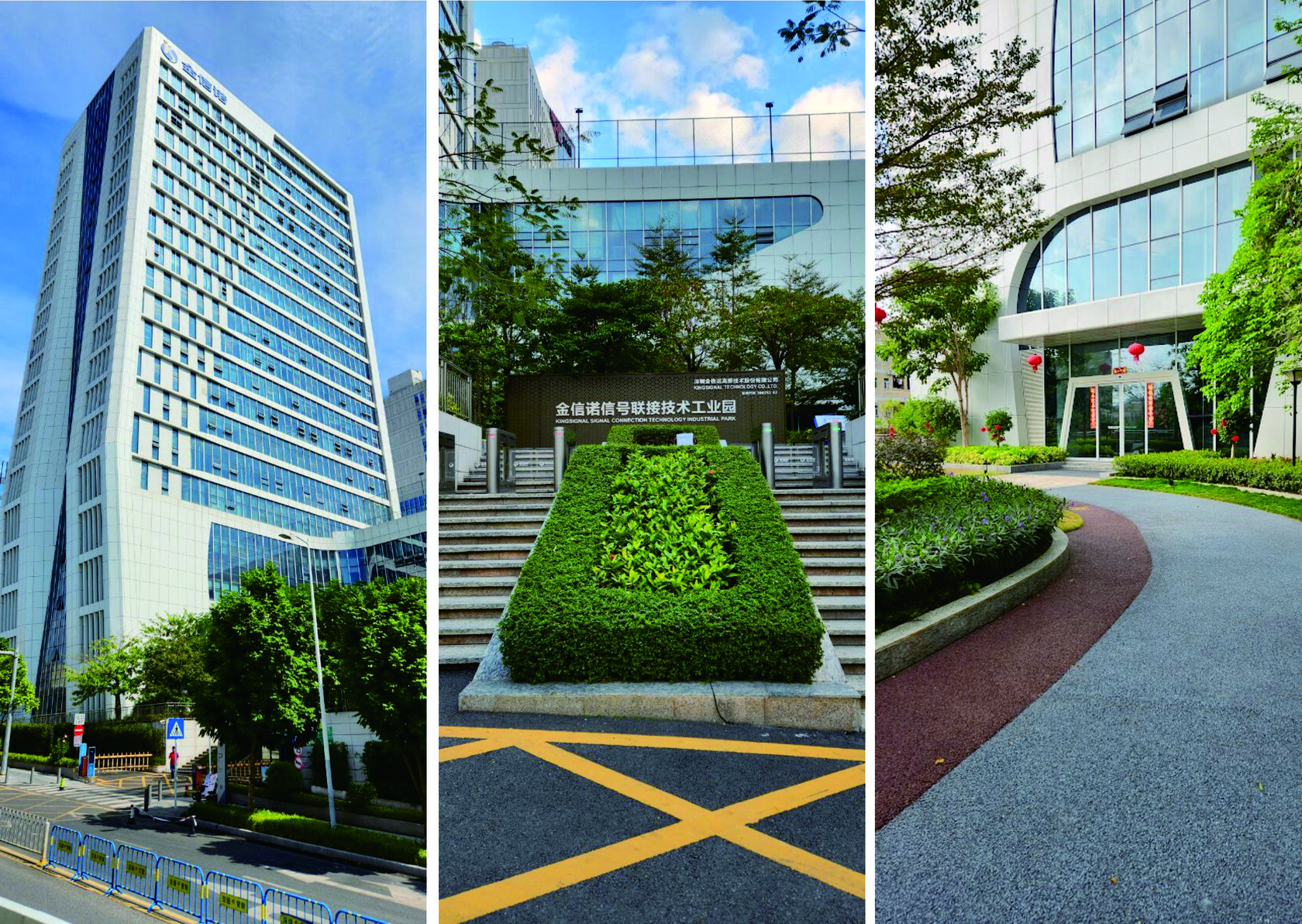
A hall inside the building with sofas and very high ceilings — nothing like a typical factory entrance.
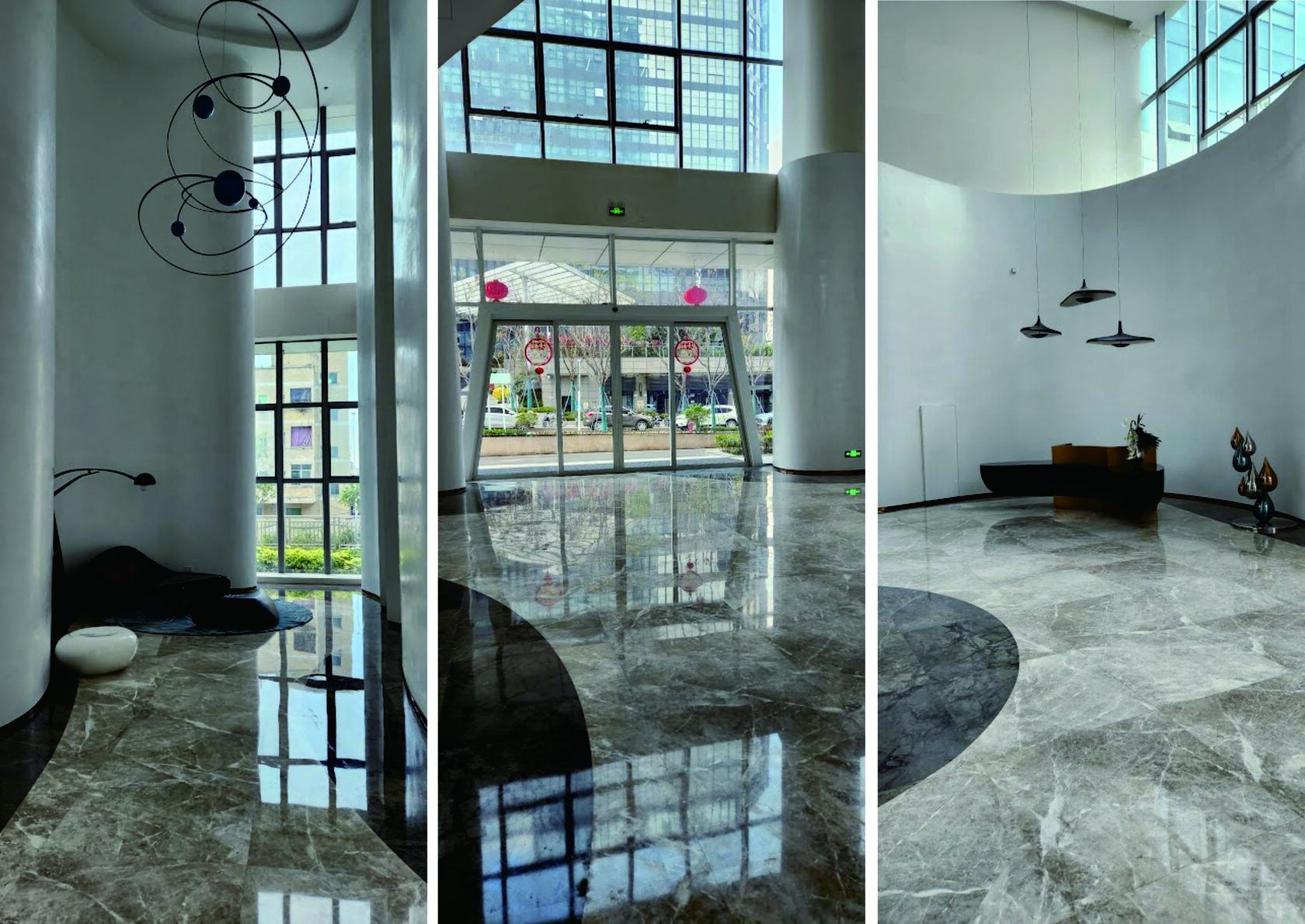
Our future office — there are some doubts about the carpet in terms of practicality, but it can easily be removed and replaced with an anti-static coating like in other assembly facilities.
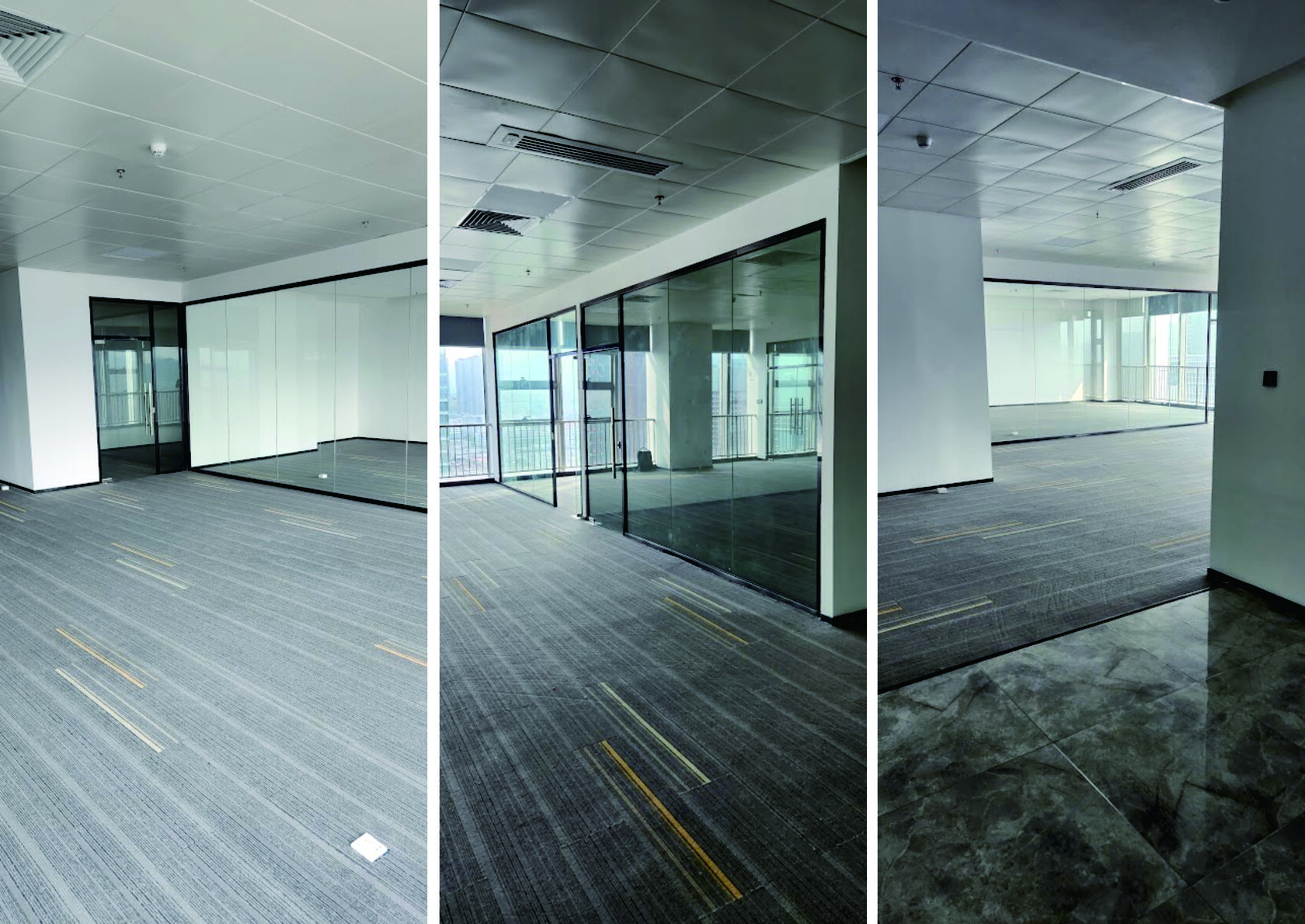
Cheers to our new office!
Nucular Team
Nucular Team